A condensing drum flaker is a specialized piece of equipment used in various industries to solidify liquid or molten substances into solid flakes. This process is crucial for handling and processing materials that need to be stored, transported, or further processed in solid form. Understanding how a condensing drum flaker works involves a detailed look at its structure, operational principles, and the processes it supports. This article delves into the functioning of it, emphasizing the critical role it plays in industrial applications.
Overview of a Condensing Drum Flaker
A condensing drum flaker consists of a rotating drum, typically made of stainless steel, which is partially submerged in a liquid or molten material. As the drum rotates, the liquid material coats the outer surface of the drum, cools, and solidifies into thin layers. These solidified layers are then scraped off the drum by a knife or blade, forming flakes. The primary function of it is to convert a liquid or molten material into solid flakes through a controlled cooling process.
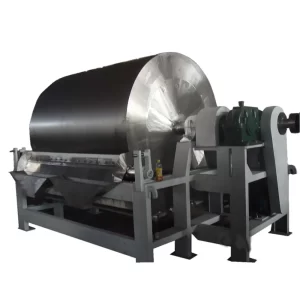
Structure and Components
- Rotating Drum: The core component of the condensing drum flaker is the rotating drum, which is usually a hollow cylinder made of a heat-conductive material such as stainless steel. The drum is designed to rotate at a constant speed, ensuring even distribution and cooling of the material on its surface.
- Heat Transfer System: Inside the drum, a heat transfer medium such as steam, hot water, or thermal oil is circulated. This system controls the temperature of the drum, allowing it to effectively transfer heat from the material to the cooling medium, thereby facilitating the solidification process.
- Liquid Feed System: The liquid or molten material is supplied to the drum through a feeding mechanism, typically involving a dip tray or spray nozzles. The material is fed in a controlled manner to ensure uniform coverage on the drum’s surface.
- Scraper Blade: As the drum rotates and the material solidifies, a scraper blade, positioned against the drum’s surface, removes the solidified layer. This blade must be precisely aligned to ensure efficient flake production without damaging the drum’s surface.
- Discharge System: The flakes scraped off the drum are collected in a discharge system, which may involve conveyors, bins, or other collection mechanisms. The flakes can then be further processed, packaged, or transported for use in other applications.
Operating Principles of a Condensing Drum Flaker
The operation of a condensing drum flaker is based on the principles of heat transfer and phase change. Here’s a detailed breakdown of the process:
- Material Feeding: The process begins with the introduction of the liquid or molten material to the drum’s surface. The material is either sprayed onto the drum or the drum is partially submerged in the material. The goal is to achieve an even coating of the material on the drum’s surface.
- Heat Transfer and Solidification: As the drum rotates, the material on its surface is rapidly cooled by the heat transfer medium inside the drum. The temperature difference between the material and the drum surface causes the material to solidify into a thin, uniform layer. This step is critical, as it determines the thickness and quality of the flakes produced.
- Flake Formation: Once the material has solidified, the scraper blade removes it from the drum’s surface in the form of flakes. The thickness of the flakes can be controlled by adjusting the drum’s temperature, rotational speed, and the position of the scraper blade.
- Discharge and Collection: The flakes are then discharged from the drum and collected for further processing. Depending on the specific application, the flakes may undergo additional steps such as drying, grinding, or packaging.
Advantages of Using a Condensing Drum Flaker
They offer several advantages in industrial applications:
- Efficiency: The continuous operation of the drum flaker allows for the efficient conversion of large volumes of liquid or molten material into solid flakes. This makes it ideal for high-capacity production environments.
- Uniformity: The controlled cooling process ensures that the flakes produced are uniform in thickness and quality, which is essential for subsequent processing steps.
- Versatility: They can handle a wide range of materials, including chemicals, pharmaceuticals, and food products. This versatility makes them valuable in various industries.
- Ease of Operation: The relatively simple design of it, combined with its automated operation, makes it easy to use and maintain. This reduces the need for extensive operator training and minimizes downtime.
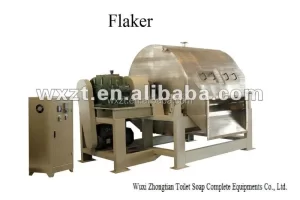
Applications of Condensing Drum Flakers
They are used in a variety of industries where the conversion of liquids to solids is necessary. Some common applications include:
- Chemical Industry: In the chemical industry, they are used to solidify chemicals such as waxes, resins, and fatty acids. The flakes produced can be easily stored, transported, and further processed.
- Pharmaceutical Industry: The pharmaceutical industry utilizes condensing drum flakers to produce flakes of active pharmaceutical ingredients (APIs) and other compounds. These flakes are often used in the formulation of tablets, capsules, and other dosage forms.
- Food Industry: In the food industry, they are employed to produce flakes of food additives, flavorings, and other ingredients. These flakes are often reconstituted or processed into other food products.
- Petrochemical Industry: The petrochemical industry uses it to process materials such as bitumen, paraffin, and other hydrocarbon-based products. The flakes are used in a variety of applications, including road construction, waterproofing, and lubrication.
Factors Affecting the Performance of a Condensing Drum Flaker
Several factors influence the performance of a condensing drum flaker, and understanding these factors is crucial for optimizing the flaking process:
- Material Properties: The physical and chemical properties of the material being processed, such as viscosity, melting point, and thermal conductivity, affect how well it can be flaked. Materials with low viscosity and high thermal conductivity are typically easier to process.
- Drum Temperature: The temperature of the drum must be carefully controlled to ensure efficient heat transfer and proper solidification. If the drum is too hot, the material may not solidify properly; if it’s too cold, the flakes may be too thick or brittle.
- Drum Speed: The rotational speed of the drum affects the thickness of the flakes and the overall efficiency of the process. A faster rotation may produce thinner flakes, while a slower rotation can result in thicker flakes.
- Scraper Blade Position: The position and angle of the scraper blade are critical for ensuring that the flakes are removed cleanly from the drum without damaging the surface. The blade must be precisely aligned to achieve the desired flake thickness and quality.
- Cooling Medium: The choice of cooling medium (steam, water, or thermal oil) and its flow rate play a significant role in the heat transfer process. The medium must be capable of absorbing the heat from the material efficiently to achieve the desired solidification.
Conclusion
In conclusion, the condensing drum flaker is a vital piece of equipment in industries that require the transformation of liquid or molten materials into solid flakes. Its operation is based on the principles of heat transfer and phase change, with the rotating drum and heat transfer system playing central roles. They offer numerous advantages, including efficiency, uniformity, versatility, and ease of operation. Its applications span across various industries, from chemicals and pharmaceuticals to food and petrochemicals. Understanding the factors that affect its performance is essential for optimizing the flaking process and ensuring high-quality output.
The condensing drum flaker continues to be an indispensable tool in modern manufacturing, providing a reliable and effective solution for the solidification and processing of various materials. As technology advances, further improvements in design and operation will likely enhance the capabilities and efficiency of this critical equipment.